Lean methodology achieves zero waste to landfill for Trivium Packaging
Mil-tek helped Trivium Packaging deliver on its environmental credentials!
Trivium reduced the internal transport by 60%
Trivium Packaging has partnered with Mil-tek at its factory to implement lean methodology beyond the production line and achieve zero waste to landfill.
And as a bonus, internal transport and time spent on waste transport was drastically reduced.
0%
“Zero waste to landfill” goal
Trivium Packaging manufactures metal packaging to help leading brands protect their products and stand out on store shelves. One of the key cultures in its Nottinghamshire plant is to push for lean manufacturing. The goal of this latest project was to help bring the company to ‘zero-waste-to-landfill’, to help deliver on its environmental credentials.
As part of the assembly of the product, components are brought in, all packaged in paper, cardboard boxes, shrink wrap and plastic banding. This resulted in a large amount of ancillary waste that goes along with the actual product that they use in manufacture.
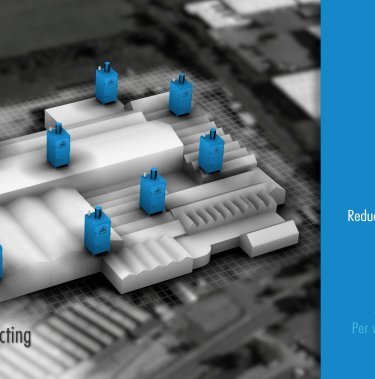
Trivium Packaging had frequent use of forklifts and piles of waste
Within production, operators had to use forklift trucks to move the waste from A to B, which resulted in piles of waste being left out on the production line for collection, as well as a lot of fork truck activity.
This proved to be an ongoing concern as the plant was always looking to reduce any possible interaction between pedestrians and fork trucks.
Although operators were tasked with keeping the working area clean, they were often obliged to either leave the production line to deal with the continuous flow of waste or allow it to pile up in the work area. Not being on the line also meant that they were not executing their core functionalities.
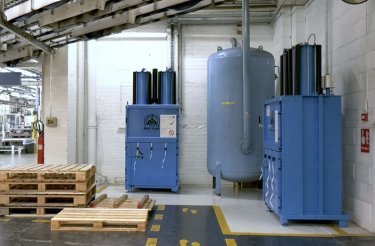
Processes and movements
The Safety Team at Trivium brought in Mil-tek to address this challenge. To do this, Mil-tek ran extensive value stream mapping on the plant to observe the production process and operator movements. Recognising the lean manufacturing culture at the plant, they showed how the existing ideology of 5S could extend beyond the production line.
The value stream mapping revealed that during a typical shift, each operator would leave the production line over 10 times and walk 300 metres across fork truck routes to an external waste container. This journey time away from the production line was seen as an unnecessary waste and eliminating this process was seen as key to addressing the overall issue. Mil-tek showed how their pneumatic waste separating technology could be used to compact this ancillary waste at source, eliminating the travel time and removing the mess.
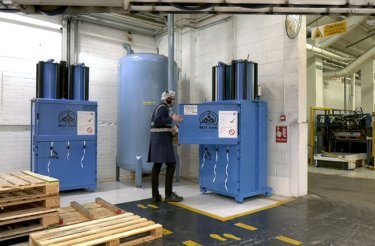
Easy install
The compaction equipment provided by Mil-tek reduced volumes by on average 10:1, thereby reducing the need for external trips to remove the packaging. Having no electrical or hydraulic components, the Mil-tek machines could be installed on the production line to maximise efficiency and be powered by compressed air lines already in place in the factory.
The deployment of the proposed solution has had a significant impact: double-digit journeys per shift fell to just one per month.
An exercise in 5S had become something more significant, with added benefits: operators were leaner, accident risk was reduced, and waste costs began to fall.
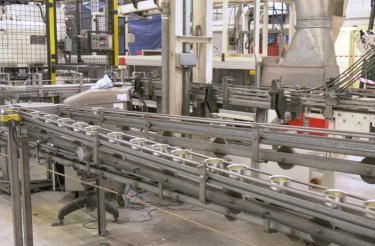
Extra benefits
Since the initial success and wider roll-out, the Mil-tek solution has been adopted in six locations around the plant, helping Trivium get nearer to achieving zero waste to landfill.
What started as a plan to reduce unsightly waste has led to cost reduction, improved efficiency, reduced carbon footprint, fewer forklift truck movements, fewer waste trucks on the premises, and more satisfied operators.
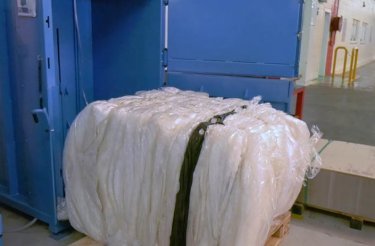
Have a question?
Get in touch today to learn more about how Mil-tek can help your business save time, space and money by better handling waste
Get info about a product or have a chat with one of our local reps. Let us know what you need so the right person can get in touch