Lean waste management
A Lean approach to waste management helps to minimize the material handling processes that do not create value. Lean waste management saves businesses time, space and money, by improving efficiency
Inefficient waste management practices
In many businesses, it is typical to collect waste or recycling materials, such as cardboard and plastic, in small containers all around the facility. These are indicated in the picture on the right as small, blue dots.
Several times a day, the waste must then be collected and transported to one or more outdoor containers, where it must be further sorted and processed by folding or cutting and once more loading into a container or compactor.
This results in an interrupted and inefficient workflow. There is a higher probability of incorrect sorting and a higher risk of internal accidents, particularly when material is transported by Fork Lift Truck (FLT).
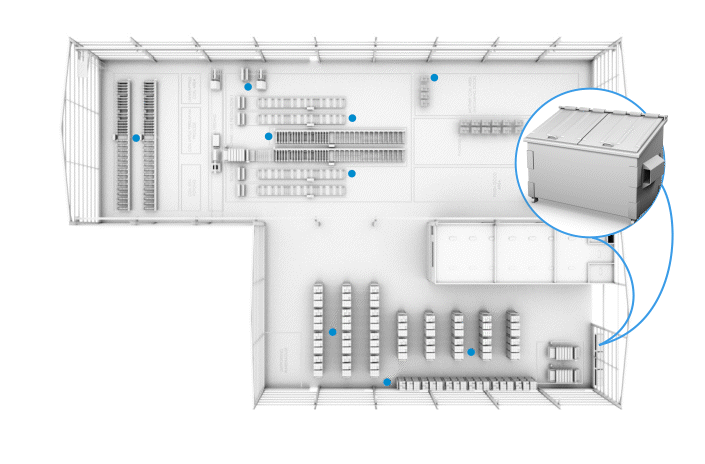
Standard external waste containers have several disadvantages
When companies use external waste containers for waste collection, there are several disadvantages:
• A lot of wasted time in connection with the transport of material to external container area and additional loading time
• Uncompacted cardboard, plastic EPS (Polystyrene) take up unnecessary space and mean more containers or expensive collections
• Constant collection costs: the container is emptied regardless of whether it is full or not
• Wrong material in the wrong container! Incorrect sorting means additional cost
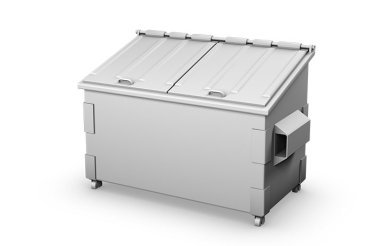
The Lean approach is about streamlining workflows by eliminating unnecessary processes, reducing internal and external trips and making continuous improvements.
Lean processes are standard within production environments, but can also be used to great benefit within other industries.
Advantages of Lean waste management
Mil-tek uses Lean principles when we tailor waste solutions. With a waste management solution based on Lean principles, our compressed air driven waste compactors are located right where the waste occurs, as close to the unpacking area as possible – as shown in the picture to the right.
The waste can then be handled immediately, directly in a cardboard baler or plastic baler, without the need to fold it or “walk with it” to a container. In the baler, the waste is compacted up to 90%. It is emptied safely and easily when it indicates a full bale. The compacted bales can be easily stored and later picked up for recycling.
The result of Lean waste management is a much more efficient work flow, where you save large amounts of time and space on your waste management, as well as saving costs for containers and collections.
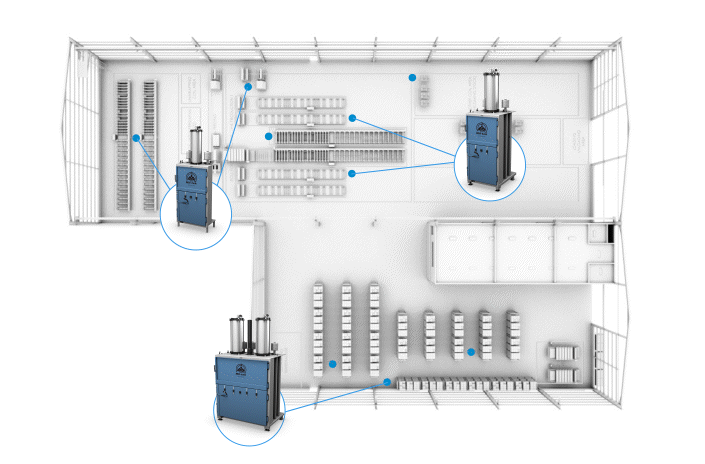
Lean waste management minimizes Forklift Truck use
Occupational accidents related to Forklift Truck driving are frequent, and in many cases such accidents lead to serious consequences. The risk of accidents with FLT driving becomes greater if there is a mix of pedestrian and driving traffic, made worse when there is clutter in the transport area.
A Lean approach to waste management, where waste is compacted at the waste source, significantly reduces the need for Forklift truck driving and results in higher safety levels.
Reduce trips by truck by 10:1
By compacting material before transporting it, your trips can move 10 times more material when it is compacted. Reducing trips by this number reduces accidents, improves efficiency and saves costs.
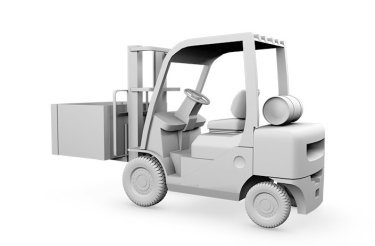
4 important Lean principles
Here you can get an insight into 4 basic Lean principles, which Mil-tek primarily uses when we tailor a waste solution for you.
“Kaizen” – continuous improvements
It’s about making constant improvements involving the whole team. Many companies use ‘Kaizen boards’ to manage the progress of new Kaizen ideas to improve efficiency.
“8 types of waste”
TIMWOODS! A great way to remember the 8 sources of waste: Time, Inventory, Motion, Waiting time, Overproduction Over-processing, Defects, Skills.
“Value Stream Mapping”
Mapping production flows or other processes with a view to identifying areas that can be improved or made more efficient.
“5S” – a tool for creating system and order
Sort, Set in order, Systematic cleaning, Standardize, Self-discipline. By working with 5S you can achieve: Better ergonomics, improved working environment, higher quality, time saving, increased productivity, employee well-being, etc.
– A sixth ‘S’ has now been added: Safety; All of the above are to be carried out in a safe working environment.

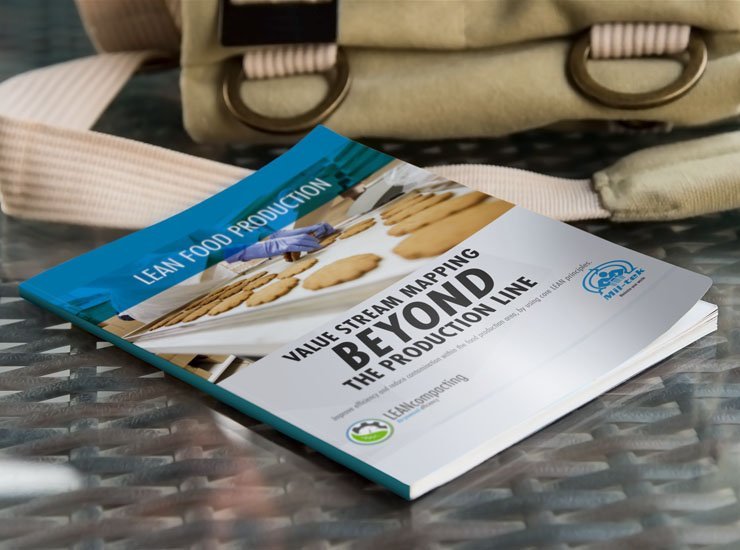
Want to know more about Lean?
Have you become curious about how you can optimize your waste management after the Lean approach, thus gaining a lot of benefits and savings?
Contact us via the form here and we will return soon.